
To make the motor shaft turn, first, one electromagnet is given power, which magnetically attracts the gear's teeth.
#L293d motor driver circuit diagram wikipedia driver#
The electromagnets are energized by an external driver circuit or a micro controller. Stepper motors effectively have multiple "toothed" electromagnets arranged around a central gear-shaped piece of iron. Each pulse moves the shaft through a fixed angle. The stepper motor is known by its property to convert a train of input pulses (typically square wave pulses) into a precisely defined increment in the shaft position. Connect them to power (normally small servos are 5V) and data (a pwm signal). Reduction gears give the motor a lot of torque (rotation force), since most of the times very high speeds are not necessary. Normally servos only cover a rotation range (180 degrees), but the closed loop allows for a fine positioning. Thesemotors consist of a closed loop system with some reduction, all paired to a dc motor. Probably the most popular h-bridge chip is the L293. If direction switching is needed an h-bridge configuration is a common solution. Lots of commercial chips can be used to substitute this. If no direction control is required a simple commuter/amplifier in parallel with a protection diode is sufficient. For higher speeds/less maintenance application brush-less motors can be used.ĭue to the back emf a driver is of some kind is required.

The brushes wear out with time and need replacement. Normally the torque is quite small and the speed is very high.

This motors are designed for a specific max voltage and current rate. We will only cover DC motors.Īn internal commutation mechanism ensures polarity switching in the coil and thus perpetual rebellion: movement.
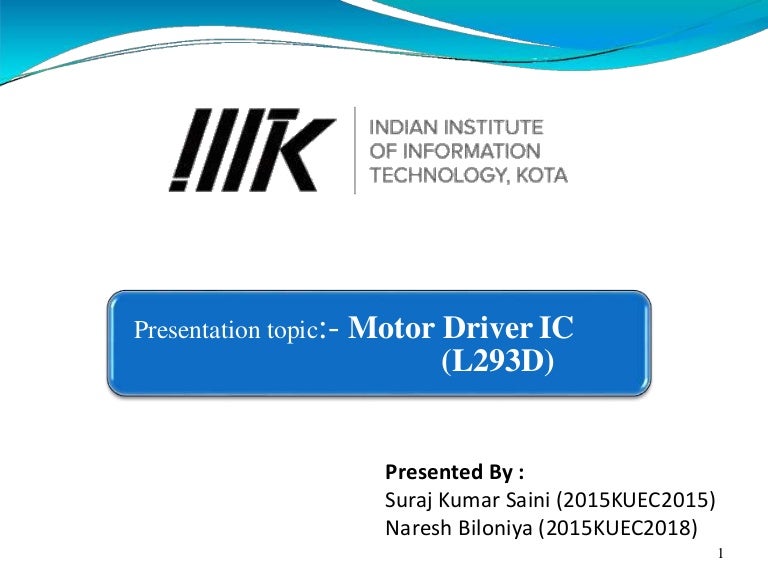
Electric motors can be classified according to the kind of current they are designed for.
